Understanding Electroplating Systems: A Comprehensive Guide
Introduction to Electroplating
Electroplating is a process that uses electrical current to reduce dissolved metal cations so that they form a coherent metal coating on an electrode. This technique is widely used in various industries to enhance the properties of metal surfaces, including corrosion resistance, wear resistance, and aesthetic appeal. Understanding how electroplating systems work is essential for industries ranging from automotive to electronics.
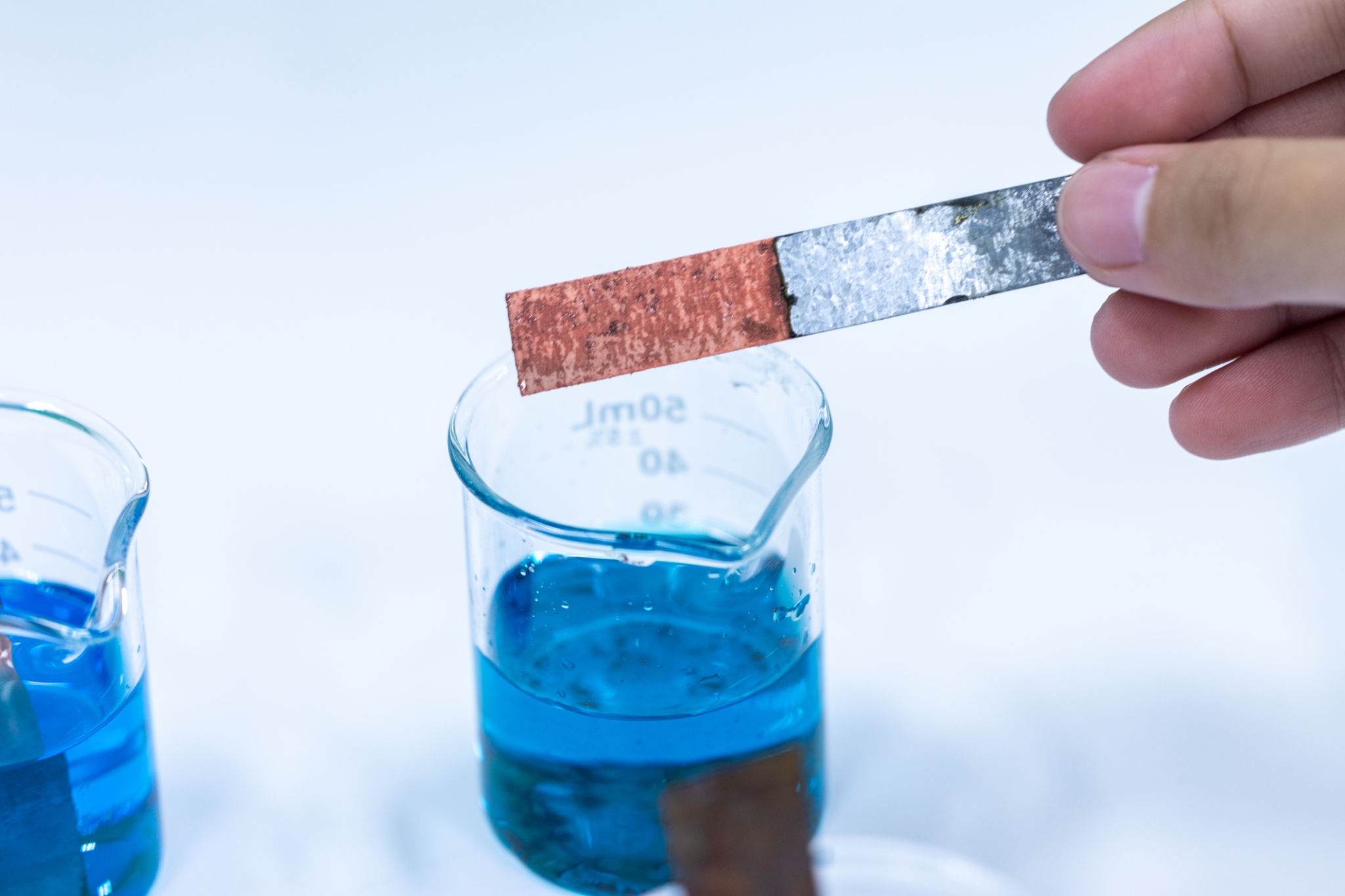
The Basics of Electroplating Systems
At its core, an electroplating system consists of three primary components: a power supply, a plating bath, and electrodes. The power supply provides the necessary electrical current, while the plating bath contains the electrolyte solution with metal ions. The electrodes include the anode, usually made of the plating metal, and the cathode, which is the object to be plated.
The process begins as the electrical current passes through the solution, causing metal ions in the electrolyte to migrate to the cathode surface. This results in a thin layer of metal being deposited onto the cathode, forming a new surface layer. This layer can be controlled in terms of thickness and uniformity, depending on the system's parameters.
Types of Electroplating
There are several types of electroplating techniques, each designed for specific applications. Barrel plating is used for small parts, while rack plating is suitable for larger items. Brush plating allows for selective plating on localized areas. Understanding the differences between these methods helps in choosing the right technique for a particular application.
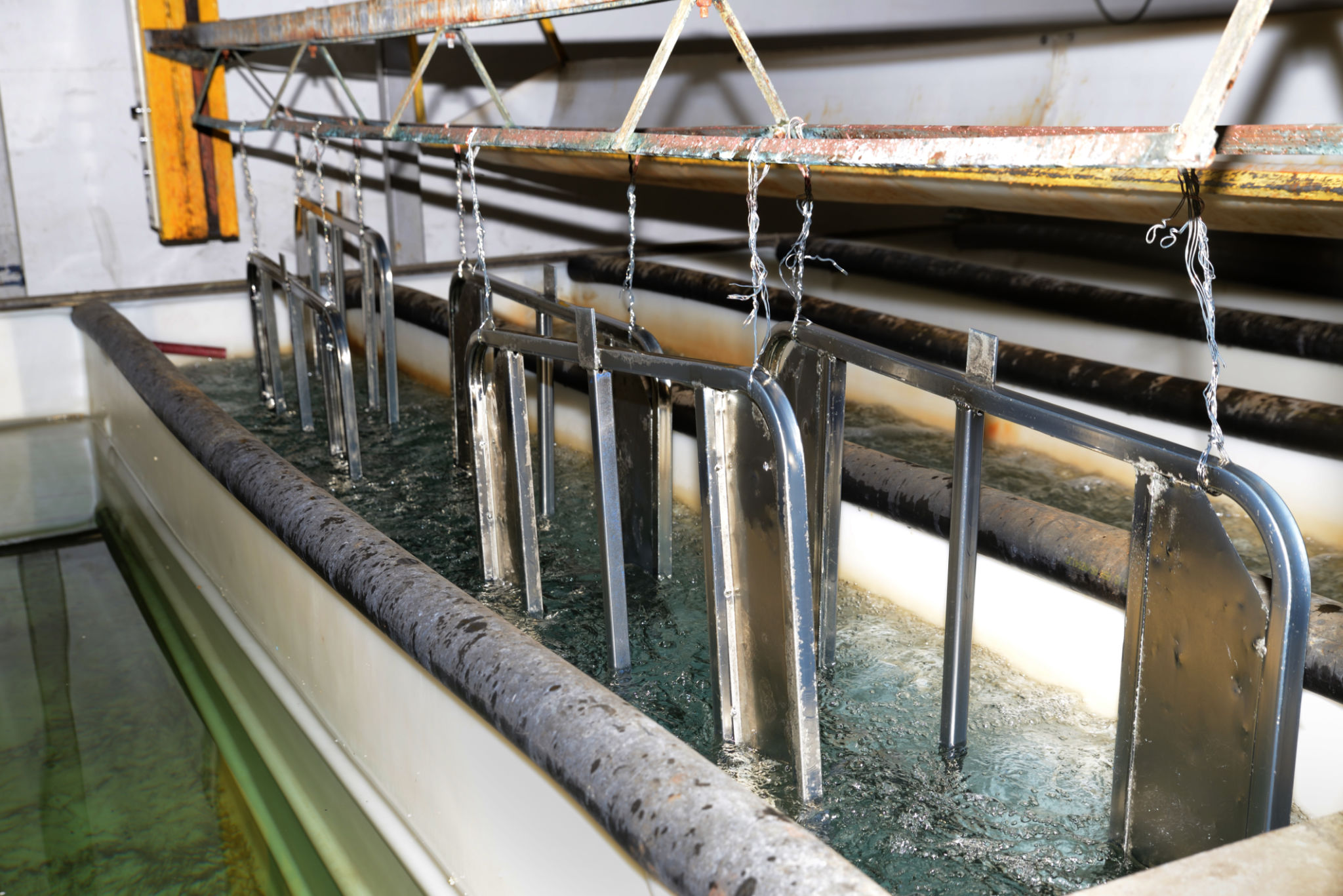
Key Benefits of Electroplating
Electroplating offers numerous benefits, making it an invaluable process in manufacturing. One of the most significant advantages is enhanced corrosion resistance. By applying a protective metal coating, components are shielded from environmental factors that cause rust and degradation.
Additionally, electroplating can improve wear resistance, extending the life of components that experience friction or contact with other materials. It also enhances aesthetic appeal, providing a shiny, attractive finish that is desirable in consumer products.
Applications Across Industries
Electroplating is used in various industries due to its versatility and effectiveness. In the automotive industry, it helps in protecting parts from harsh conditions and improving their appearance. The electronics industry uses it for creating conductive surfaces on circuit boards. Jewelry manufacturers rely on electroplating for decorative purposes, ensuring longevity and beauty in their products.
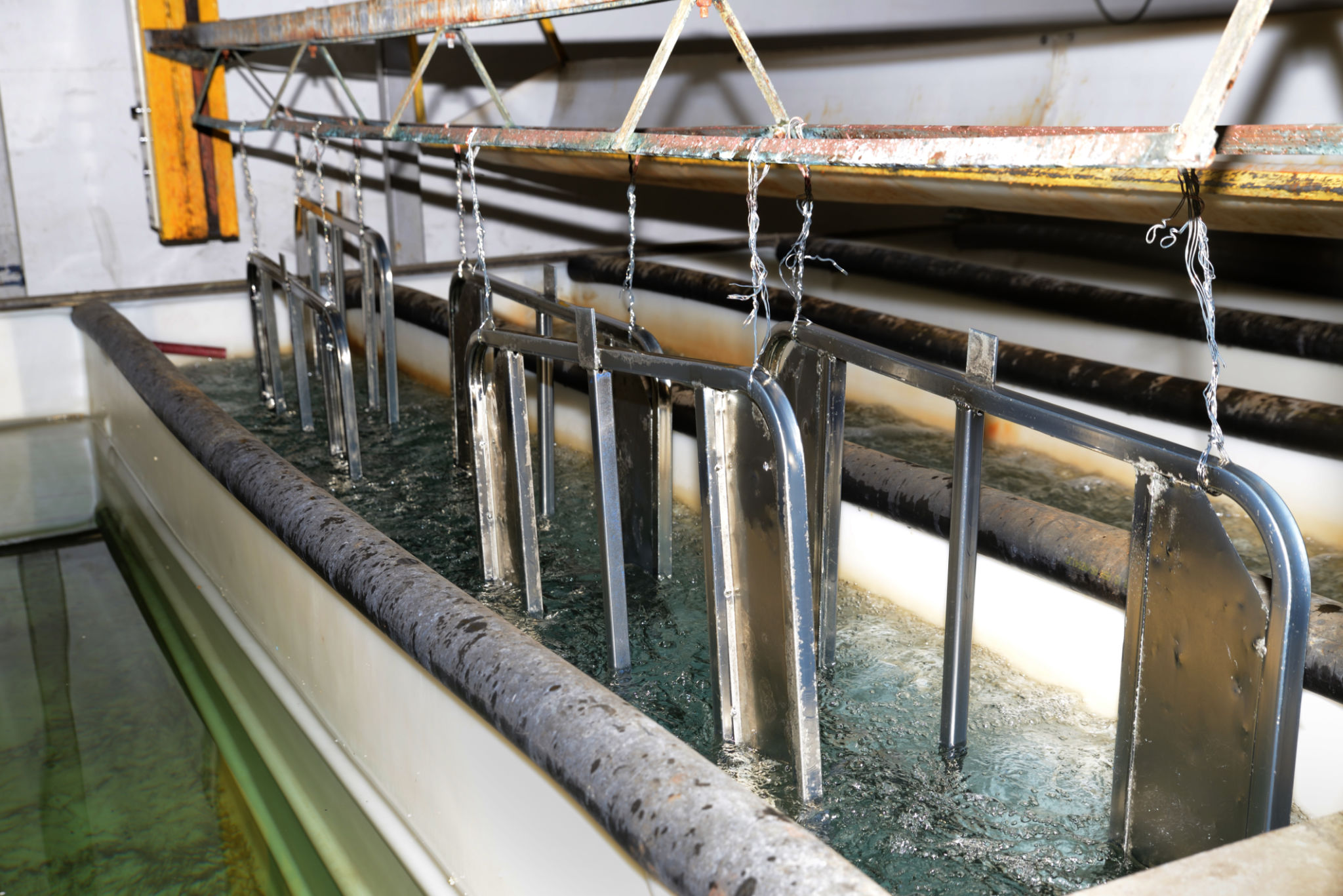
Challenges and Considerations
While electroplating is beneficial, it also presents certain challenges. Environmental concerns are significant due to the chemicals used in the process. It's crucial to implement proper waste management and recycling techniques to minimize environmental impact.
Another consideration is the need for precise control over plating parameters such as current density, temperature, and plating time. These factors directly affect the quality and consistency of the plated layer.
Future of Electroplating Technology
The future of electroplating lies in advancements that make the process more efficient and environmentally friendly. Research is ongoing to develop new electrolyte solutions that reduce toxic waste and improve energy efficiency. The integration of digital technologies for precise control and monitoring is also paving the way for smarter electroplating systems.
As industries continue to seek ways to improve product quality and sustainability, electroplating will undoubtedly evolve, offering even greater benefits across various applications.
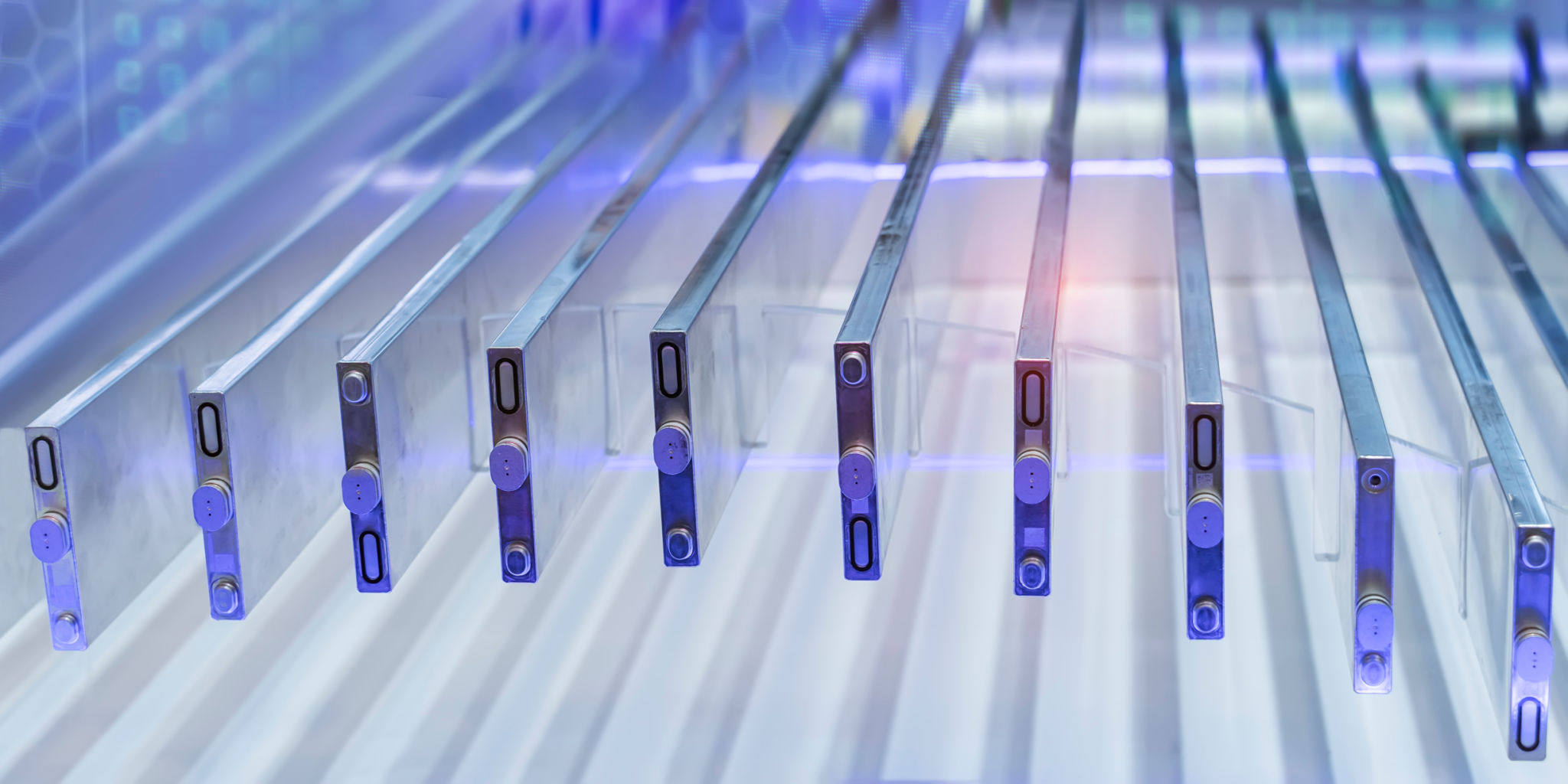