Comparing Surface Treatment Technologies: Which is Best for You?
Understanding Surface Treatment Technologies
Surface treatment technologies play a crucial role in enhancing the performance, appearance, and longevity of materials. With numerous options available, choosing the right technology can be challenging. Each method offers distinct advantages that cater to specific applications, making it essential to understand their differences.
In this blog, we will compare some of the most popular surface treatment technologies, including electroplating, powder coating, anodizing, and plasma treatment. By understanding their unique benefits and limitations, you can make an informed decision about which technology is best suited for your needs.
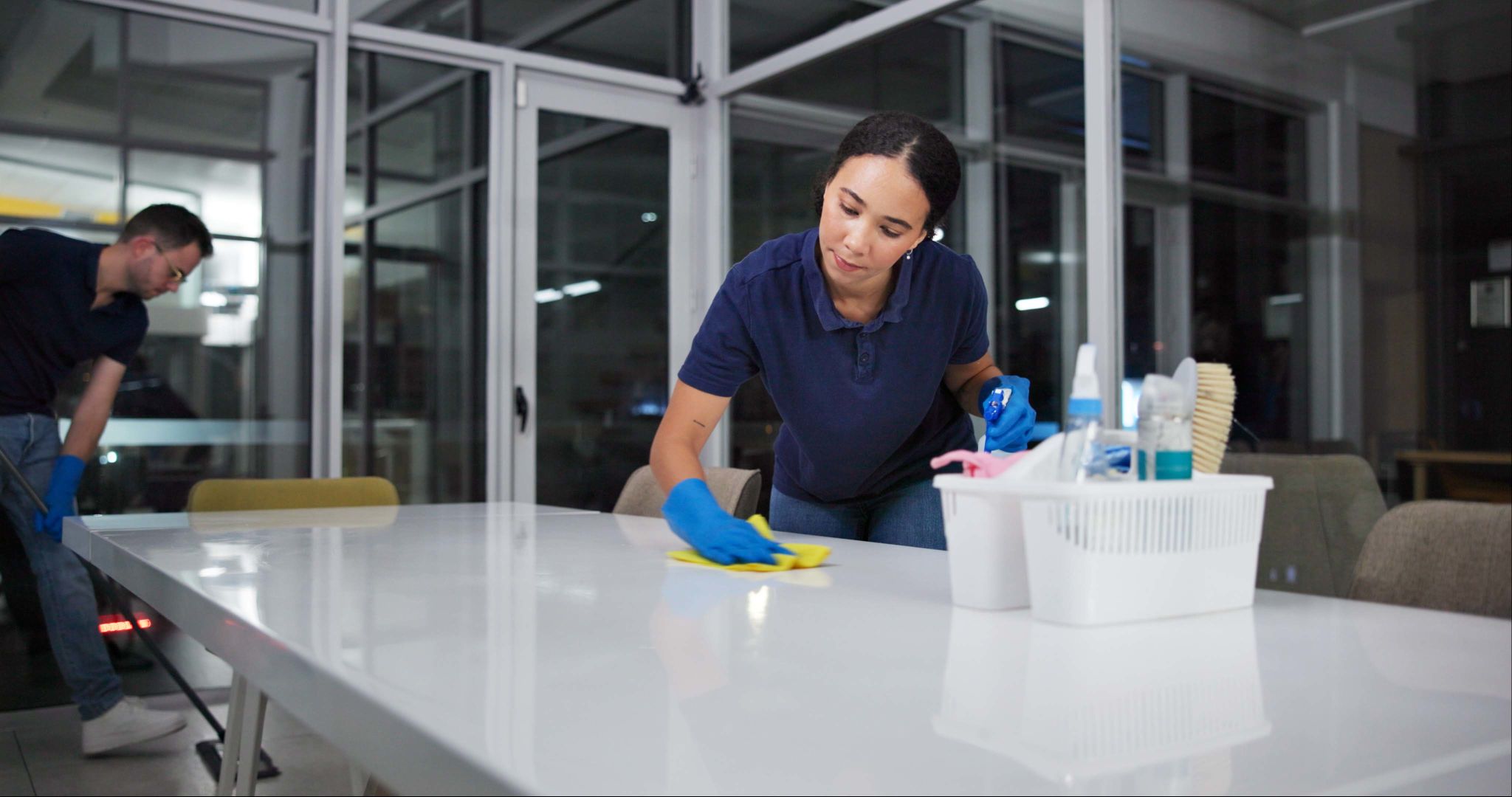
Electroplating
Electroplating is a widely used surface treatment process that involves depositing a thin layer of metal onto a substrate. This method is highly effective for improving corrosion resistance, enhancing electrical conductivity, and achieving a decorative finish. Common metals used in electroplating include nickel, chromium, and gold.
This technique is ideal for applications requiring precision and uniform coating. However, it may not be suitable for all materials, as some substrates can be prone to hydrogen embrittlement during the process. Additionally, electroplating requires careful waste management due to the chemicals involved.
Powder Coating
Powder coating is a dry finishing process that applies a free-flowing powder onto a surface, which is then cured under heat to form a durable coating. This method is praised for its environmental friendliness, as it produces minimal waste and emits no volatile organic compounds (VOCs).
Powder coating offers excellent resistance to chipping, scratching, and fading, making it ideal for outdoor applications. However, it may not be as effective for achieving ultra-thin coatings compared to other methods. The initial setup cost can also be higher due to the need for specialized equipment.
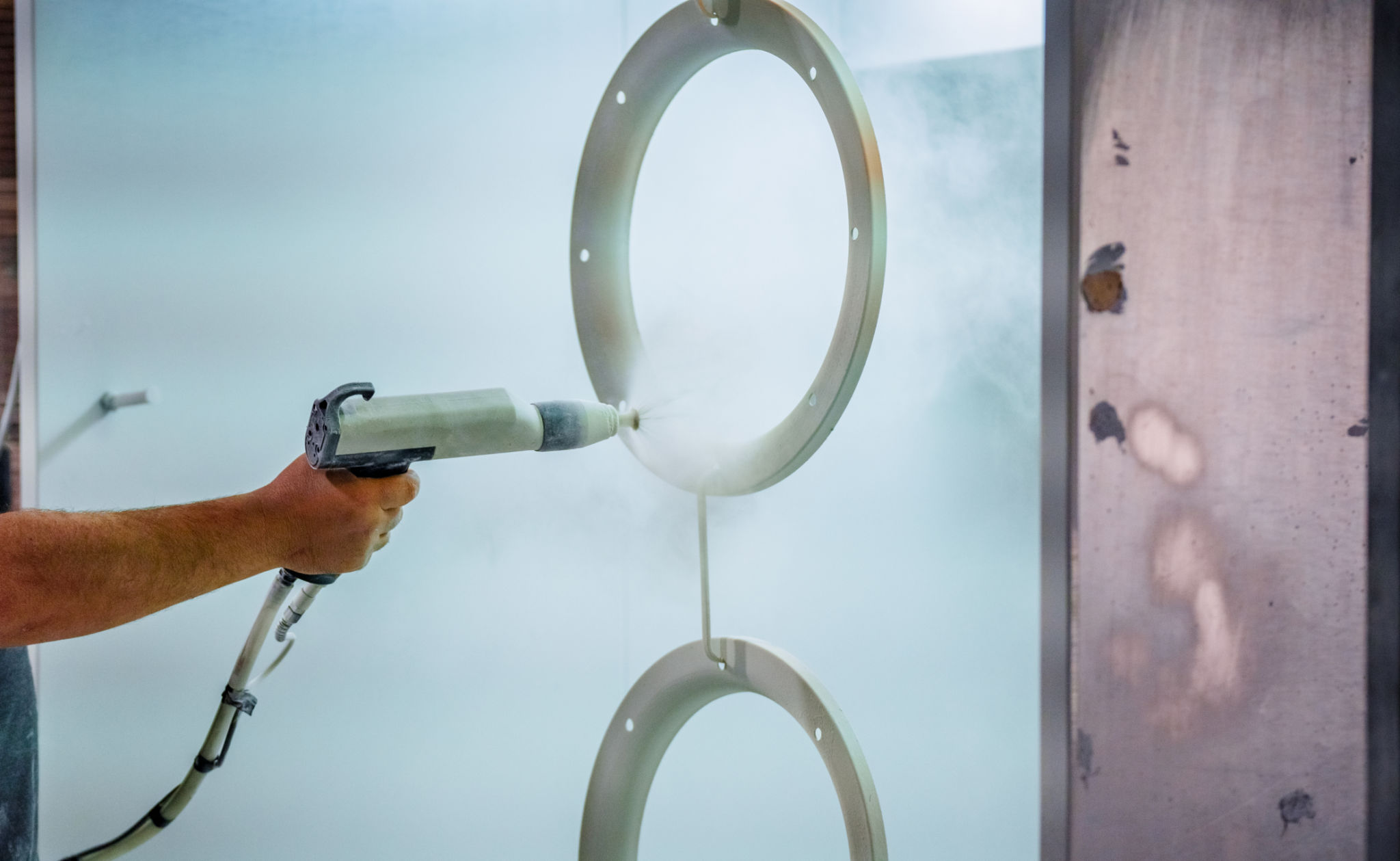
Anodizing
Anodizing is an electrochemical process that converts the surface of a metal, typically aluminum, into a durable, corrosion-resistant oxide layer. This process not only enhances the aesthetic appeal but also increases the surface hardness and wear resistance of the material.
One of the significant advantages of anodizing is its ability to maintain the natural metallic appearance while offering various color options. However, anodized surfaces can be prone to scratching if not handled properly. It is also limited primarily to aluminum and a few other metals.
Plasma Treatment
Plasma treatment is an advanced surface modification technique that uses ionized gas to alter the properties of a material's surface. This method can improve adhesion, wettability, and biocompatibility without altering the bulk properties of the material.
Plasma treatment is highly versatile and can be applied to a wide range of materials, including plastics, metals, and ceramics. It is often used in industries such as medical devices and electronics. However, it requires specialized equipment and expertise to perform effectively.
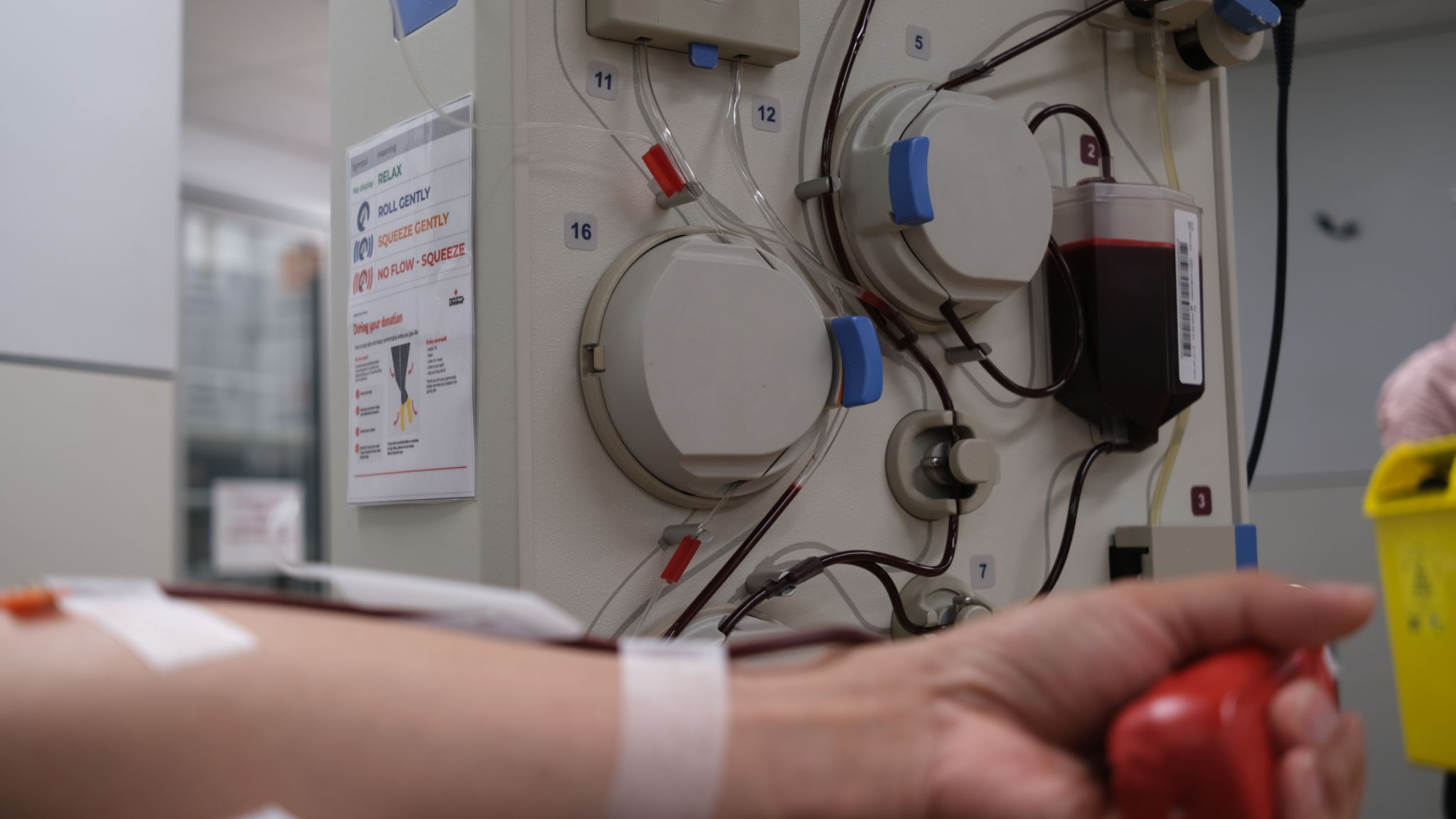
Choosing the Right Technology
When selecting a surface treatment technology, consider factors such as the material type, desired properties, environmental impact, and cost. Each method has its unique advantages and limitations that can influence your decision.
- Electroplating: Best for precise and uniform coatings on conductive materials.
- Powder Coating: Ideal for durable, eco-friendly finishes with excellent resistance.
- Anodizing: Suitable for enhancing aluminum surfaces with decorative and protective layers.
- Plasma Treatment: Versatile option for improving surface properties across various materials.
By analyzing your specific needs and requirements, you can choose the most appropriate surface treatment technology that aligns with your goals. Consulting with experts in the field can also provide valuable insights to ensure optimal results.